PP/PS/EVOH Sheet Extrusion Line
Short Description:
product description our certificates FAQ request a quote Menu product description our certificates FAQ request a quote The PP PS sheet extrusion line developed by Jwell is used to produce multi-layer composite environmentally friendly sheets. The sheet mainly blisters various food containers and packaging, such as trays, noodle bowls, lunch boxes, cake boxes, and fruit trays. The equipment can effectively use the proportion of stone powder, reduce the cost of sheet material...
Product Detail
Product Tags
The PP PS sheet extrusion line developed by Jwell is used to produce multi-layer composite environmentally friendly sheets. The sheet mainly blisters various food containers and packaging, such as trays, noodle bowls, lunch boxes, cake boxes, and fruit trays.
The equipment can effectively use the proportion of stone powder, reduce the cost of sheet material, improve the degradability of the sheet, and ensure the comprehensiveness of the sheet.
PP PS feature introduction and industrial application
PP——polypropylene is a kind of lightweight thermoplastic synthetic resin with excellent performance, chemical resistance, heat resistance, electrical insulation, high-strength mechanical properties, and good wear-resistant processing properties.
After PP undergoes chemical modification, physical modification, and transparency modification, the colorability, processability, and impact resistance will become better.
PP has a wide range of applications: fiber products (clothing, blankets), auto parts, chemical containers, food, and drug packaging, etc.
PS-polystyrene, including ordinary polystyrene, expanded polystyrene (EPS), high-impact polystyrene (HIPS), and syndiotactic polystyrene (SPS).
Ordinary polystyrene is a colorless and transparent particle with excellent heat insulation, insulation, and transparency, and easy to color.
Application areas: building materials industry, automobile industry, packaging industry, etc.
PP sheet has high transparency, good barrier properties, low density, non-toxic and hygienic, and can be recycled and will not produce toxic and harmful gases when heated and burned.
Mainly used for packaging and stationery of food, medicine, medical equipment, etc., such as processed jelly boxes, dairy product packaging boxes, cold drink containers, fast food boxes, microwave oven appliances, stationery tablets, folders, etc.
PS is similar to PP in performance, and it also performs well in food packaging. Because of its low static electricity generation, it is mostly used in electronic product packaging.
PP PS sheet extrusion line model selection
In the current market, the PP PS sheet extrusion line is mostly single-screw models, because the equipment cost is much lower than that of twin-screw models.
Jwell’s PP/PS single-screw model has stable feeding and can plasticize the raw materials well under a variety of different formulations, ensuring the toughness of the sheet and avoiding the easy heat forming of the sheet in the later stage. Problems such as cracking and uneven color.
In the production of PP sheets, the Jwell single-screw model is currently capable of stable production up to 1.5 tons per hour.
Although the cost of the twin-screw model is higher, it is better than the single-screw in other aspects.
Twin-screw, the design flexibility of its thread structure is stronger, which ensures the extruder’s feeding, and at the same time makes the formula material have better dispersion in the barrel, and the sheet material will be more uniform.
PP PS sheet extrusion line equipment features
1.Whether it is a single screw or a twin screw, there is a design that meets the production of PP and PS at the same time.
The single-screw machine lengthens the ratio of length to diameter and increases the vacuum exhaust;
The twin-screw machine adds a vacuum system to ensure the full discharge of material water vapor and ensure the performance of the sheet.
2.The winding adopts two structures of traditional winding machines or a fully automatic winding machine to meet the needs of customers for ordinary small-volume production and large-capacity production, and directly help customers reduce labor costs.
In addition, the fully automatic winding machine has no jamming in the cutting of thick sheets, and there is no phenomenon that it cannot be wound.
3.The efficient and stable control system makes the pressure and speed of the PP PS sheet extrusion line more stable.
The precise control system makes the equipment more comfortable in improving the output and performance of the equipment.
PP PS sheet extrusion line control system
The PP PS sheet extrusion line adopts Siemens frequency conversion, servo control, and Ethernet transmission technology control to achieve high efficiency, high precision, high stability, and high safety.
The 100M/s high-speed network transmission reduces the error caused by the transmission between the control system and the drive and makes the equipment more efficient.
HMI man-machine interface, centralized control system, realizes one-screen browsing of the whole machine system parameters, such as current, pressure, speed, temperature, etc., making the operation easier.
Structure composition of PP PS sheet extrusion line
J-type three-roll stand-alone sheet machine production line:
The unit is mainly composed of a host, a screen changer, a melt pump, a mold, a tablet press, a conveyor table, a tractor, a cutting machine or a winder, etc.;
The reduction box body is made of cast steel, the gears are made of alloy steel, and have been ground teeth. The lubrication points in the box body are all forced to lubricate. The lubricating oil is equipped with a cooling water system.
The screw material is made of 38CrMOA1A nitrided steel, which has been nitrided, and the surface is sprayed with alloy.
The material of the barrel is 38CrMOA1A nitrided steel, which has been nitrided, and the surface is sprayed with alloy.
The raw materials that can be processed are PP, PE, PS, ABS, etc.;
J-type three-roll multi-machine co-extrusion sheet production line:
The unit is mainly composed of a host, a screen changer, a mold, a three-layer distributor, a tablet press, a conveyor table, a tractor, a cutting machine or a coiler, etc.;
The reduction box body is made of steel castings. The gears are made of alloy steel and have been ground teeth. All lubrication points in the box body are forced to lubricate. The lubricating oil is equipped with a cooling water system.
The screw material is made of 38CrMOA1A nitrided steel, which has been nitrided, and the surface is sprayed with alloy.
The material of the barrel is 38CrMOA1A nitrided steel, which has been nitrided, and the surface is sprayed with alloy.
The raw materials that can be processed are PET, PP, PE, PS, etc.
Hierarchical structure: AB, ABA, ABBA, etc.
Mainly applicable to stationery (such as folders), blister products (such as blister cups, blister boxes, etc.), advertising (such as billboards, etc.)
PP/PS/EVOH Sheet Extrusion Line Main technical parameter
Species | Suction package sheet | Stationery decoration sheet |
Product thickness | 0.18-2.0mm | 0.15-2.0mm |
Product width | 600-1500mm | 600-1500mm |
Raw material | PP/PS/HIPS/EVOH | PP/PS/PE |
Output | 200-1000Kg/h | 200-1000Kg/h |
PP/PS/EVOH Sheet Extrusion Line Application
PP Barrier (EVA, EVOH) Sheet Co-Extrusion Line
The multi-layer sheet is used for creating high barrier packaging containers commonly used in Aseptic, Hot Fill, and Retort packaging applications. With the capability to extrude up to 7-layers, it can create both roll stock and containers with very strong oxygen and moisture vapor transmission protection for product sensitive and long-term shelf life applications.
PP/EVA/EVOH multi-layer sheet co-extrusion line
To meet the market’s high request for products, Suzhou JWELL developed advanced technology of five layers symmetrical distribution and seven layers asymmetrical distribution, which makes the produced sheets having better barrier performance,
excellent anti-oxygen, and anti-humidity. Mainly used for Jelly packing, meat packing, snack food packing and etc, medicine and cosmetic packing.
PP/PS package sheet 、stationery decoration sheet extrusion lines
PP/PS sheet is widely used for food, electrical component package;differehnt kinds of sand, transparent, inclined grain decoration sheet. We are able to supply multilayers sheet extrusion machines as the customer’s requirements, the output range is from 100-1200kg/h for option.
Application and machine photo
PP/PS/EVOH Sheet Extrusion Line Technical Specification
Model: JWS120-1000 1 layer Extrusion Sheet Line
General:
1.Suitable material: PP/PS pellet
2.Utility source:
Electric Power Supply All Cabinets including main cabinet and control cabinets and all internal cables will be supplied by the seller, buyer’s responsibility is for external cables and cable frame to main panel/input power position of sheet extrusion machine)
Mains input 3×380V (Volt)
Fluctuation max ≦+/-15%
Frequency 50HZ
Fluctuation max +/-1.5HZ
Cooling water supply: used on machinery in closed or open-loop circuits must have the general requirement: clean filtered and free of sediments.
Supply temperature 30℃
Supply pressure 4-6bar
Pressure variation +/-0.5bar
Return pressure average 1.5bar
Consumption capacity 20-25m3/h
Compressed air supply: clean, free of oil, dust, and water.
Supply pressure at the point of use ≧7bar
Pressure variation +/-1%
Consumption capacity 0.9 m3/h
3.Technical Data:
Extruder (JWS120/33):
Max output: 300-400KG/H
Product width 1000mm
Final sheet thickness 0.2-1.2mm
Effect width of die 1150mm
Effective width of roller 1200mm
Roller diameter Φ400/500/400mm
Equipment list:
- JWS120/33 feeding system 1set
- JWS120/33single screw extruder 1set
- Hydraulic screen changer 1set
- Melting Pump 1set
- T-die(Jwell brand) 1set
- Three-roller calender 1set
- Roller temperature controller 1set
- Cooling bracket 1set
- Side trimming unit 1set
- Haul off unit 1set
- Double position Winder 1set
- Electric control system 1set
- Spare parts list 1set
Specification:
1.JWS120/33feeding system
500kg vertical stirrer 1 unit
600kg/h vacuum loader 2 units
1000kg/h hot air dryer 1 unit
150kg hopper 1 unit
vertical stirrer2.JWS120/33single screw extruder
screw and barrel:Domestic famous brand JINHAILUO®, founded in the year 1978.
Material: 38CrMoAlA
Nitrided layer thickness:0.5-0.7mm
screw hardness: HV>=740
barrel hardness: HV>=940
L/D: 33:1
Screw diameter: 120mm
Heating zones: 7 zones
Total power: About 50KW
Heating method: Ceramic heater
Cooling method: Air cooling
Drive Motor: Siemens Beide AC motor
Inverter: ABB inverter
Drive Power: 132KW
Gearbox origin: High quality, made in China, with cooling.
Gears type: Helical gears
Heat treatment: Carburized and grind
Connection method of motor and gearbox:Direct power-transmission via the elastic clutch.
3.Hydraulic screen changer
Using plate type double-position structure, automatically change nets
Using a high-quality alloy changer, stainless steel net changer, the heating element is overflow.
Between the connection of changer and barrel are equipped with the pressure sensor.
Use one hydraulic valves, power: 4kg, both oil pump and electric are chosen high brand.
4.Melting Pump
Jwell product
Motor: local Gearbox and motor and a universal shaft connecting, motor power: 7.5KW.Danfoss inventor.
Max pressure: 25Mpa, heating by stainless steel heating robs. Before the pump is the Italian Gefron pressure sensor, can adjust the screw rmp with close loop control, keep output smoothly.
5.T-die
High-quality alloy 5CrNiMo forging die bodies materials, Clothes hanger channel, Chromium plating cavity surface polishing, processing, Ra0.02um,0.03-0.05mm HRC60-65.
Die using stainless steel heating robs, fully
integrated wiring, socket. 100mm deck is equipped
width of the die: L=1150mm
product width: L=1000mm
product thickness: δ=0.2-1.2mm
6.Three -roller calinder
Roller diameter:Φ400/Φ500/Φ400mm
Roller Length: L=1200mm
Surface roughness:Ra<=0.025um
Surface hardness:HRC55-60
Chromium coated layer thickness:0.1mm
Roller roundness and straightness:<0.01mm
Transmission type:Separate driving for 3 rollers.
Transmission:local reducer and Innovance Servo motor
Separate driving power:2.9kw*3
Gap adjustment between rollers:Open and close by mechanical, manual adjust both sides, roller distance show by a dial indicator.
Bearings for three rollers:Japan NSK
Calendar type:L type
Rotational joint:High quality, used for high temperature
Equip with a protection device, when the operator touches the button, three rollers will stop.
7.Roller temperature controller
Cooling medium:water
Temperature range:35-100℃
Temperature control precision:<=+/-1℃
Heating unit:electric heater
Water pump:Stainless steel multistage Pumps.
Water power:3×4Kw
Electromagnetic valve:pneumatic valve with angle.
Be with alarm function for pressure, temperature, and water shortage, etc.
8.Cooling supporting frame, side trimming unit
Length:6m
Cooling supporting frame:aluminum rollers, oxidized, polished.
Specification:Ф70x1200mm
9.Side trimming unit
Type: blade cutting
Edge trim cutter:2 pieces of knives
10.Haul off unit
Rubber roller material:Steel+Nitride rubber
Roller material: 45# steel with plating treatment
Roller Number:1 Pair
Specification:Ф250mm×1200mm
Power:3kw
Transmission:local reducer and Inovance Servo motor
It can be controlled synchronously with the three rollers or separately.
Trimming winding system 1set
With tension control
11. Doubleposition Winder
Type: adopt servo motor type winder
Auto meter counter: Korea brand
Air shaft: 3 inches
Max. winder diameter: 600mm
12. Electricity control
HMI SIEMENS
PLC: SIEMENS
Button, switch, indicator: Schneider or Chint brand
Air switch: Schneider brand
Relay : IDEC/ABB/Schneider brand
Contactor: Schneider brand
Spare part list
- Screw Knock-down tool 1set
- Mould knock-down tool 1set
- 3M Thermal couples 5 pairs
- 5M Thermal couples 5 pairs
- 120 extruder heating band 1pc
- 120 extruder cooling fan 1pc
- Brass ruler 2pcs
- Heating band for roller 3pcs
- Mould heating band 4pcs
- Heating band for screen changer 4pcs
- edge cutting knives 10pcs
- Contacts 2pcs
- Air switches 2pcs
- Non-force alu. Roller 1pc
- hex wrench 1set
- metal hose 3pcs
After-sale service
- The guarantee period is 1 year and service is available lifelong.
- Our expert will answer any inquiry within 24-48 hours and it will be solved as soon as possible.
- The customer can send the engineer to our JWELL with training.
- The Seller supplies the complete technical support documents and the relative drawings of the electric components written in Chinese and English.
- 5. List of the spare parts (Please see the list of spare parts)
Video
PP/PS/EVOH Sheet Extrusion Line running in Turkey customer factory

FAQ
- International Commercial Terms(Incoterms): FOB, CFR, CIF, EXW
- Terms of Payment: LC, T/T
- Average Lead Time: Peak season lead time: 3-6 months, Off season lead time: 1-3 months
- Number of Foreign Trading Staff:>50 People
Yes, We own 5 manufacturing bases and sales center in Shanghai , Suzhou ,Changzhou, Zhou Shan, Dongguan China.
Jwell made the first Chinese screw and barrel in 1978 in brand name Jinhailuo.After more than 40 years development,
JWELL is one of the biggest extrusion machine supplier in China with 300design&test engineer, 3000 employees.
Jwell has become the premier supplier of extrusion lines and reliable business partners. Welcome to drop in us.
Our machines taking the European standards and follow the Germany type of business, we cooperation with
International famous brands Siemens Schneider Flender Omron ABB WEG Falk Fuji etc. Our company continuously
imports over 1000 international first-class high precision processing equipment such as multistage machining centers, CNC lathes and CNC milling machines from Korea, Japan etc. All our processes strictly adhere to CE certification,
IS09001 and 2008 quality management system . And we have 12 months quality warranty time. We testing the
machine performances before each delivery. Jwell service engineers will always be here for anything you needed.
Usually it takes about 1 – 4 months depends on different machinery upon receipt of order advance payment.
Once clear your requirements and determined extrusion line is ideal for you. We will send technical solutions and
Proforma Invoice to you. You can pay via TT bank transfer, LC as you like.
One. We provide both customized extrusion lines and technical solutions. Welcome contact with us for technical
innovation or improvements for your future purchasing plan.
We produce more than 2000 advanced extrusion lines every year world wide.
We can send the small spare parts by air express for urgent matter. And the complete production line by sea
to save the cost. You can either use your own assigned shipping agent or our cooperative forwarder. The nearest
port is China Shanghai, Ningbo port, which is convenient for maritime transportation..
Yes, we support our business partners by pre-after sale service. Jwell has more than 300 technical testing
engineers traveling world wide. Any cases would be responded with prompt solutions. We provide training, testing,
operation and maintenance service for a life time.
Certificates
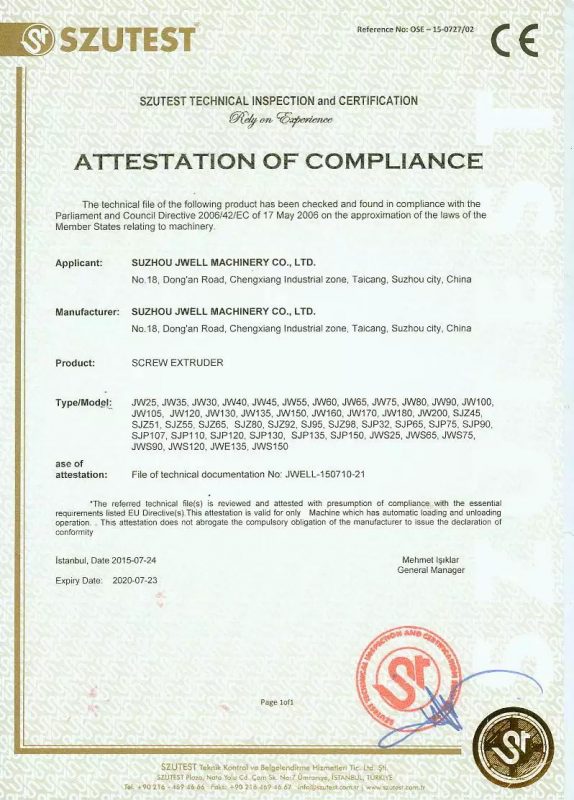
Certified By:SGS
extrusion down stream equipment
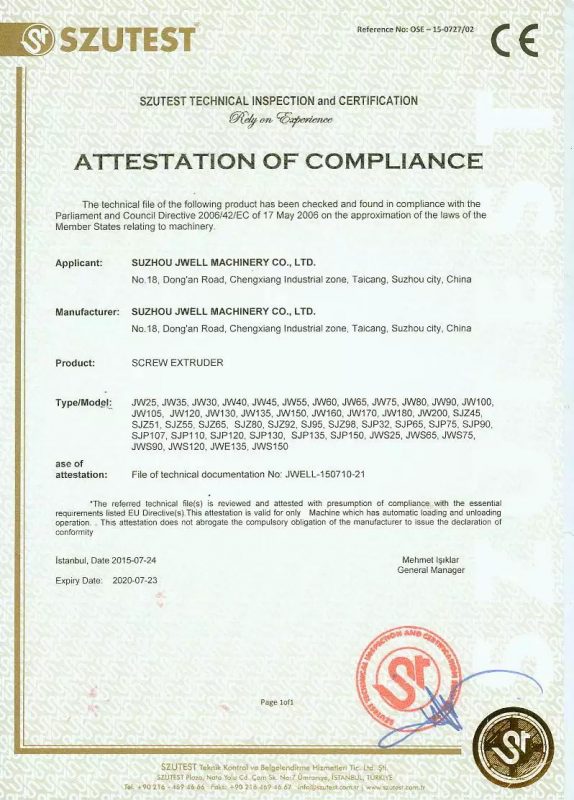
Certified By:SGS
extrusion down stream equipment
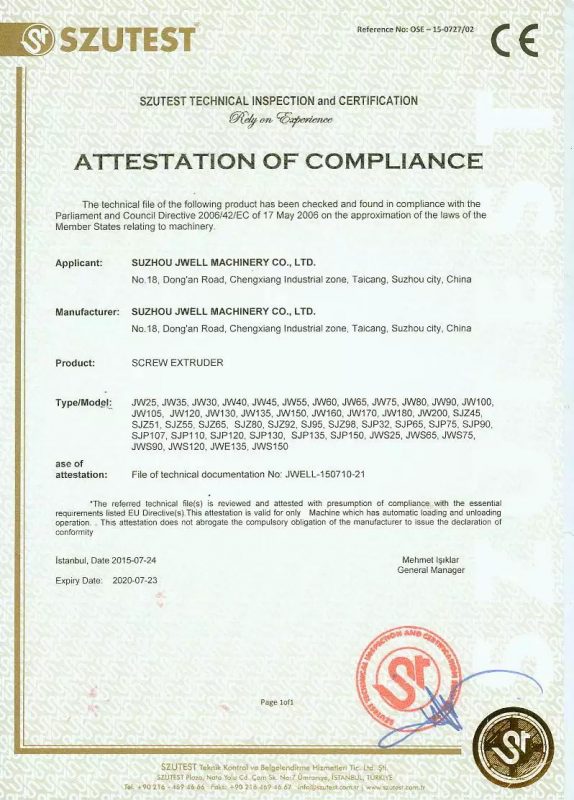
Certified By:SGS
extrusion down stream equipment
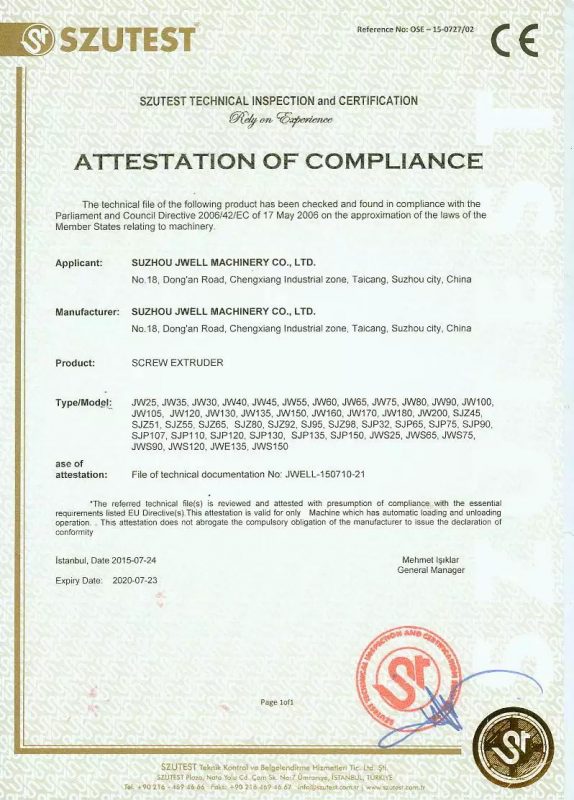
Certified By:SGS
extrusion down stream equipment
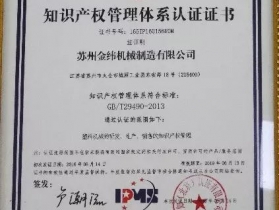
Certified By:Other
Design, Development, Manufacture and Sales of intellectual property rights management for Plastic Machine
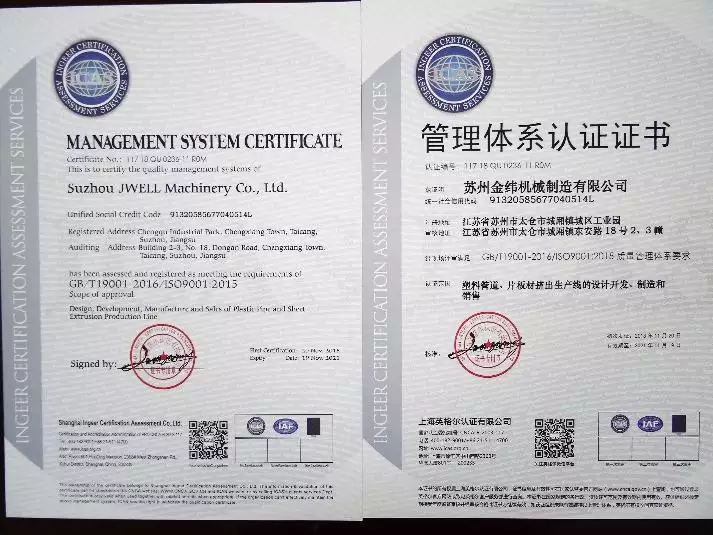
Certified By:Other
Design, Development, Manufacture and Sales of Plastic Pipe and Sheet Extrusion Production Line
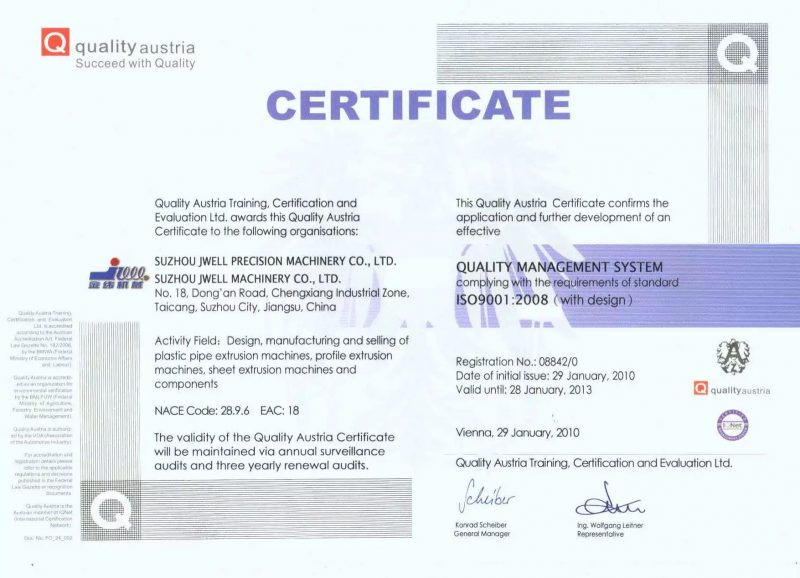
Certified By:Quality Austria Training, Certification and Evaluation Ltd
Plastic extrusion line