SMS/SMMS/SS/SSS Spunbond non-woven equipment production line
Short Description:
product description our certificates FAQ request a quote Menu product description our certificates FAQ request a quote Spunbond non-woven equipment production line description The production line adopts the direct melt extrusion spinning method of polymer, and uses the principle of aerodynamics to make the tow move in a certain flow field. The process of decelerating by air diffusion, dividing the silk and laying the net, and then consolidating the fiber net ...
Product Detail
Product Tags
Spunbond non-woven equipment production line description
The production line adopts the direct melt extrusion spinning method of polymer, and uses the principle of aerodynamics to make the tow move in a certain flow field.
The process of decelerating by air diffusion, dividing the silk and laying the net, and then consolidating the fiber net into a cloth by means of point bonding.
In spinning, the full-width slit is the drafting device. Due to the long drafting distance, the drafting air pressure is used more efficiently, which can give the tow drafting force and save energy. And the drafter is manufactured in one piece, so it does not require maintenance and repair during use.
In the aspect of splitting and laying the net, the bell-mouth air duct is used to use the diffusion and deceleration of the airflow to make the tow spiral downward in the natural state. Because the fiber is in a messy laying state, the anisotropy of the fiber is guaranteed and directly controlled. The vertical and horizontal strength, uniformity and tensile strength of the finished fabric.
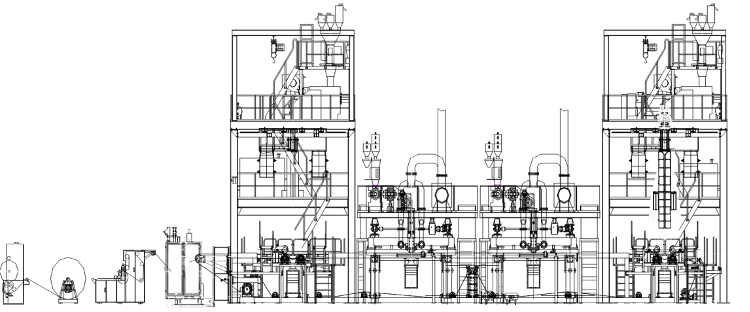
Spunbond non-woven equipment production line Major equipment
1.Metering pumps
The metering pump is an external gear pump. When the gears are in meshing operation, the gear meshing and disengagement will increase the volume of the suction chamber and form a negative pressure. The polymer melt is sucked into the pump and fills the valleys of the two gears. The melt is driven by the gear to close to the inner wall of the “8”-shaped hole and is sent to the outlet cavity after rotating for nearly a week. Due to the continuous change of the volume of the outlet cavity, the polymer melt can be discharged smoothly.
The amount of polymer melt output per revolution of the metering pump is called the nominal flow rate of the metering pump, and the ratio of the actual flow rate of the pump to the theoretical flow rate is called the volumetric efficiency of the pump. There are many factors that affect the volumetric efficiency, such as the sealing performance of the pump joint surface, the gap that causes the melt backflow, the speed, the inlet and outlet melt pressure, and the melt viscosity. The total efficiency of a gear metering pump is the product of volumetric efficiency and mechanical efficiency. For gear pumps with higher precision, the total efficiency is usually 0.90 to 0.95.
2.Spinning components
The important parts of the spinning system are composed of box, melt distribution plate, spinneret, etc. The spinning process can use a single large-scale spinneret, or it can be formed by splicing multiple small-sized plates. Moreover, rectangular plates are more commonly used, followed by circular plates.
The diameter of the spinneret hole should be determined according to the shear rate gradient of the fiber-forming polymer melt flowing in the spinneret hole. Generally, the diameter and length of the spinneret hole are larger, and the spinning is relatively stable, especially for high viscosity melts. The spinning is advantageous.
3.Cool down
This process is carried out simultaneously with the deformation of the melt trickle. The temperature of the tow extruded from the spinneret is quite high. Cooling can prevent the adhesion and entanglement between the filaments. With the stretching, the viscous melt stream gradually becomes a stable solid fiber. The spinning process often adopts the form of single-sided side blowing and double-sided side blowing. The cooling medium is clean air-conditioned air. The air volume should ensure the flow mode is a stable laminar flow state, so as to avoid the vibration of the thread and affect the uniformity of the thread. . The cooling process is accompanied by the crystallization process. In the initial stage, the temperature is too high, and the thermal motion of the molecules is too violent. With the decrease of temperature, the speed of homogeneous nucleation gradually increases, the viscosity of the melt increases, the mobility of the chain segment decreases, and the crystal growth speed decreases.
experience:
Air supply temperature: 15~16℃(±1℃)
Supply air humidity: >80%
Supply air pressure: 300~400Pa(±2%)
Cleanliness: ≤1.2μm
4.draft
1. Orientation
The length of linear polymers is hundreds, thousands, or even tens of thousands of times its width. This structural asymmetry makes them easy to make dominant parallel arrangements in a specific direction under certain circumstances, which is called orientation. .
2. The role of drafting
The newly formed nascent fiber has low strength, large elongation and extremely unstable structure. The purpose of drafting is to align the long molecular chains of the fibers and the lamellae of the crystalline polymer along the fiber axis, thereby improving the tensile properties and abrasion resistance of the fibers, while obtaining the required fiber fineness. Drafting is the means, and orientation is the result obtained. After orientation, the temperature should be quickly dropped below the glass transition temperature of the polymer to “freeze” the orientation result and prevent de-orientation.
3. Drafting device
The main methods are roller mechanical drafting and air drafting. Most of the spinning process uses air drafting. Air drafting is the use of high-speed airflow to draft the thread friction, divided into positive pressure drafting and negative pressure drafting. There are nozzle drafting and narrow slot drafting in the form of airflow drafting, and the airflow speed can reach 3000~4000m/min or higher. The drafting device and the drafting process of different companies are very different. The recent technological breakthroughs in the spinning process, such as the increase in spinning speed and the reduction of fiber fineness, are mainly technological breakthroughs in the drafting device and drafting process.
5.Laying control
Laying control The drawn and divided filaments are laid on the condensation curtain in a certain way. There are two main control methods:
Airflow control uses airflow diffusion and Coanda effect to place filament bundles on the condensing screen in a certain way, such as circular or elliptical motion; it also uses side-blown airflow to alternately blow the filaments left and right to lay into a net.
The mechanical control utilizes the left and right reciprocating motion of the roller, rotor, swing sheet or drafting and separating pipe to lay the tow regularly on the condensation net curtain. The uniformity of the spinning process is not as good as that of the dry process. The smaller the product mass per unit area, the larger the cv value.
Spunbond non-woven equipment production line Applications
Baby diaper production
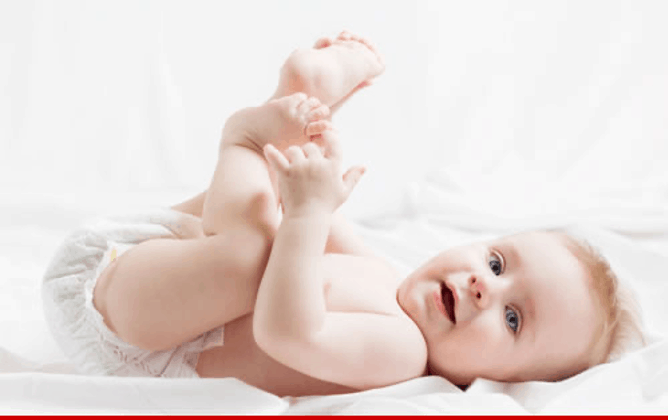
The product is made of polypropylene, which has strong hair flexibility, comfortable hand feeling, large air permeability, high water pressure resistance, high strength, and can block and isolate dust, particles, alcohol, blood, liquid, bacteria and viruses.
Application areas: Hydrophilic surface layer perforation, hydrophilic core covering, hydrophilic diaper, incontinence pad hydrophilic surface layer, super soft diaper bottom film composite
Product selection: SSMMS, SMMS, SSS, SS
Weight range: 10-25 g/㎡
Post-treatment process: hydrophilic, water repellent, super soft
Ladies hygiene products production
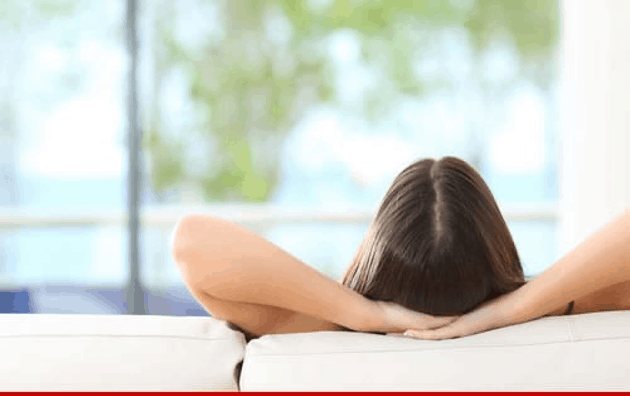
The product is made of polypropylene, which has strong hair flexibility, comfortable hand feeling, large air permeability, high water pressure resistance, high strength, and can block and isolate dust, particles, alcohol, blood, liquid, bacteria and viruses.
Application areas: Hydrophilic surface layer punching, hydrophilic core coating, super soft base film composite
Product selection: SSMMS, SMMS, SSS, SS
Weight range: 10-25 g/㎡
Post-treatment process: hydrophilic, water repellent, super soft
Surgical supplies production
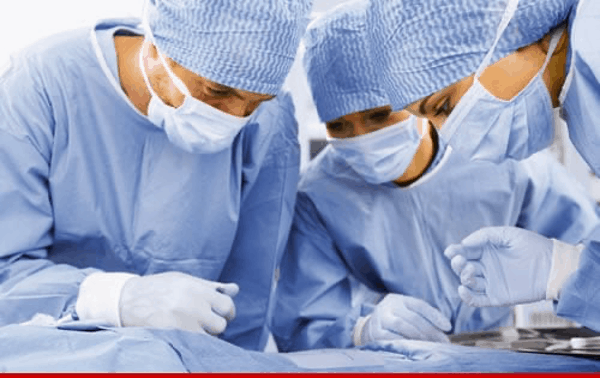
The product is made of polypropylene, which has good toughness, high filterability and softness, and has been functionally treated at the same time. It has strong functionality, large air permeability, high water pressure resistance, high strength, and can block and isolate dust. Invasion of particles, alcohol, blood, fluids, bacteria and viruses.
Application areas: Surgical caps, composite sheets, surgical gowns, surgical hole towels, visiting gowns, isolation gowns
Product selection: SSMMS, SMMS, SSS, SS
Weight range: 10-65 g/㎡
Post-treatment process: anti-static, anti-ultraviolet, anti-aging, anti-alcohol, anti-plasma, antibacterial, anti-oil, anti-mildew, etc.
Surgical instrument sterilization wrapping cloth production
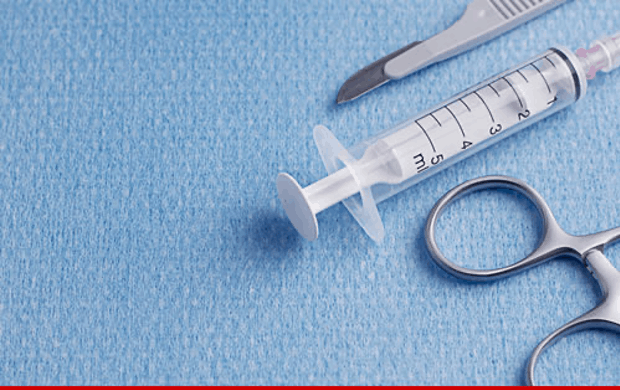
A non-woven product with high hydrostatic performance and high barrier to liquid and solid particles.
Product selection: SSMMS, SMMS, SSS, SS
Weight range: 10-100 g/㎡
Post-treatment process: anti-static, anti-ultraviolet, anti-aging, anti-alcohol, anti-plasma, antibacterial, anti-oil, anti-mildew, etc.
Shopping bag production
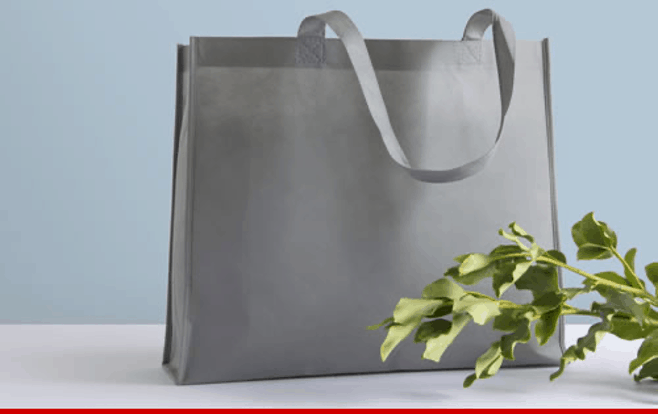
Using polyester as raw material, high temperature resistance, corrosion resistance, UV resistance, water permeability, high tensile strength, strong puncture resistance, strength proportional to weight, wide range of use, long life, and recyclability. Polylactic acid is a man-made material that can be completely degraded, degraded into carbon dioxide and water, returned to nature, does not pollute the environment, and is an environmentally friendly product.
Product selection: SS, SSS, SMS, SSMMS, PET, PLA
Weight range: 15-150 g/㎡
Clothing packaging belt production
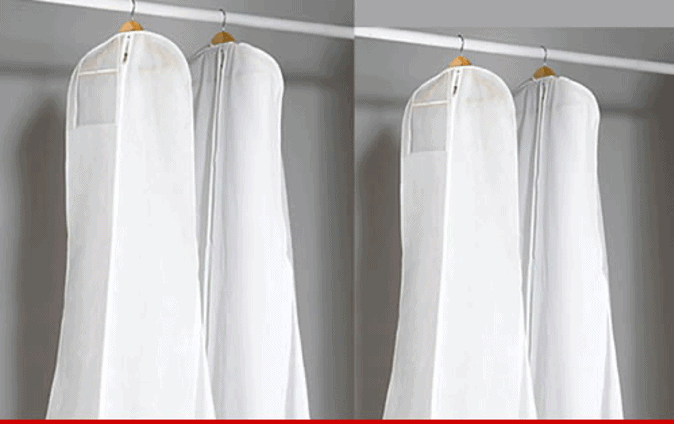
Using polyester as raw material, high temperature resistance, corrosion resistance, UV resistance, water permeability, high tensile strength, strong puncture resistance, strength proportional to weight, wide range of use, long life, and recyclability. Polylactic acid is a man-made material that can be completely degraded, degraded into carbon dioxide and water, returned to nature, does not pollute the environment, and is an environmentally friendly product.
Product selection: SS, SSS, SMS, SSMMS, PET, PLA
Weight range: 15-150 g/㎡
FAQ
- International Commercial Terms(Incoterms): FOB, CFR, CIF, EXW
- Terms of Payment: LC, T/T
- Average Lead Time: Peak season lead time: 3-6 months, Off season lead time: 1-3 months
- Number of Foreign Trading Staff:>50 People
Yes, We own 5 manufacturing bases and sales center in Shanghai , Suzhou ,Changzhou, Zhou Shan, Dongguan China.
Jwell made the first Chinese screw and barrel in 1978 in brand name Jinhailuo.After more than 40 years development,
JWELL is one of the biggest extrusion machine supplier in China with 300design&test engineer, 3000 employees.
Jwell has become the premier supplier of extrusion lines and reliable business partners. Welcome to drop in us.
Our machines taking the European standards and follow the Germany type of business, we cooperation with
International famous brands Siemens Schneider Flender Omron ABB WEG Falk Fuji etc. Our company continuously
imports over 1000 international first-class high precision processing equipment such as multistage machining centers, CNC lathes and CNC milling machines from Korea, Japan etc. All our processes strictly adhere to CE certification,
IS09001 and 2008 quality management system . And we have 12 months quality warranty time. We testing the
machine performances before each delivery. Jwell service engineers will always be here for anything you needed.
Usually it takes about 1 – 4 months depends on different machinery upon receipt of order advance payment.
Once clear your requirements and determined extrusion line is ideal for you. We will send technical solutions and
Proforma Invoice to you. You can pay via TT bank transfer, LC as you like.
One. We provide both customized extrusion lines and technical solutions. Welcome contact with us for technical
innovation or improvements for your future purchasing plan.
We produce more than 2000 advanced extrusion lines every year world wide.
We can send the small spare parts by air express for urgent matter. And the complete production line by sea
to save the cost. You can either use your own assigned shipping agent or our cooperative forwarder. The nearest
port is China Shanghai, Ningbo port, which is convenient for maritime transportation..
Yes, we support our business partners by pre-after sale service. Jwell has more than 300 technical testing
engineers traveling world wide. Any cases would be responded with prompt solutions. We provide training, testing,
operation and maintenance service for a life time.
Certificates
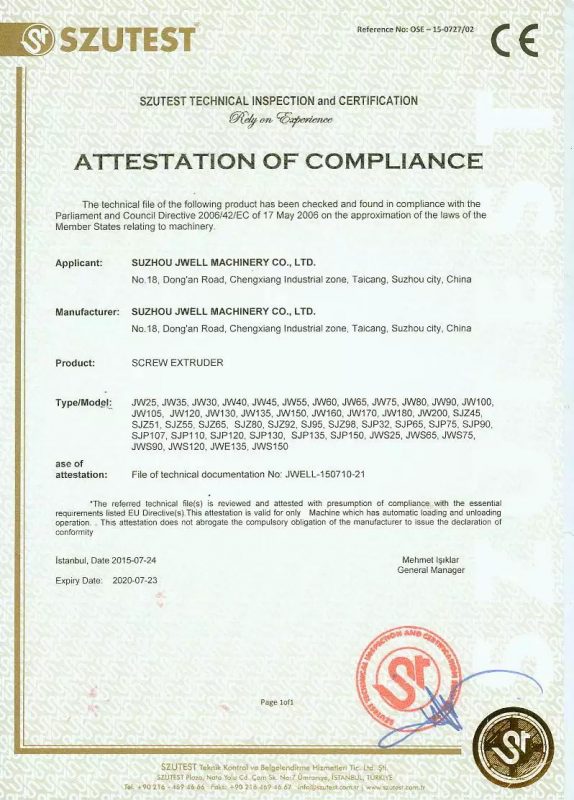
Certified By:SGS
extrusion down stream equipment
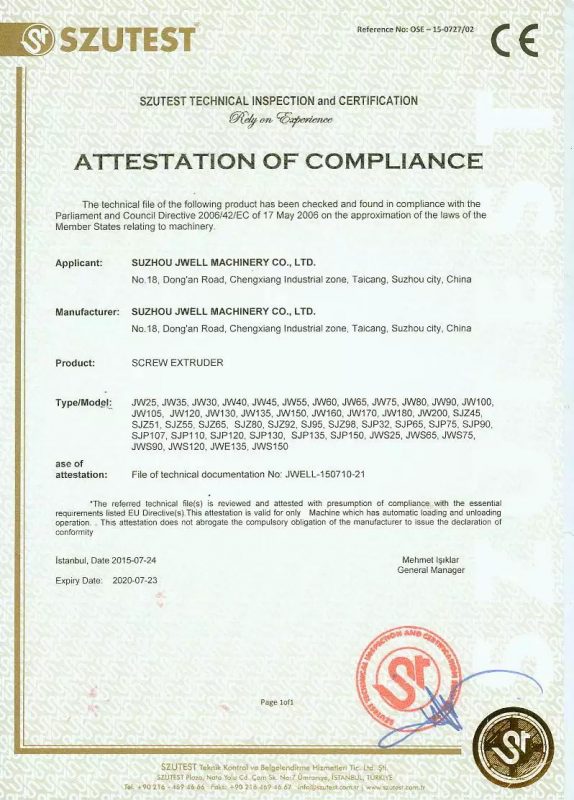
Certified By:SGS
extrusion down stream equipment
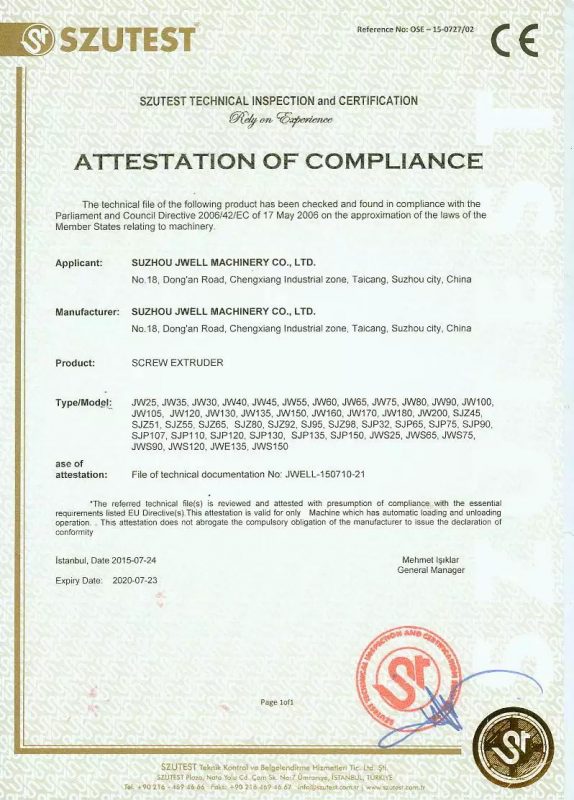
Certified By:SGS
extrusion down stream equipment
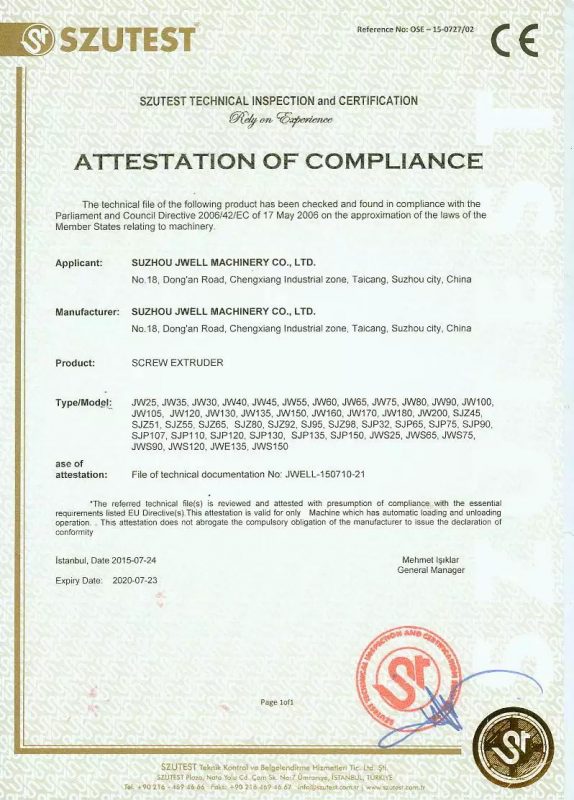
Certified By:SGS
extrusion down stream equipment
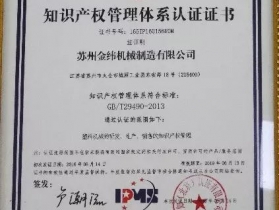
Certified By:Other
Design, Development, Manufacture and Sales of intellectual property rights management for Plastic Machine
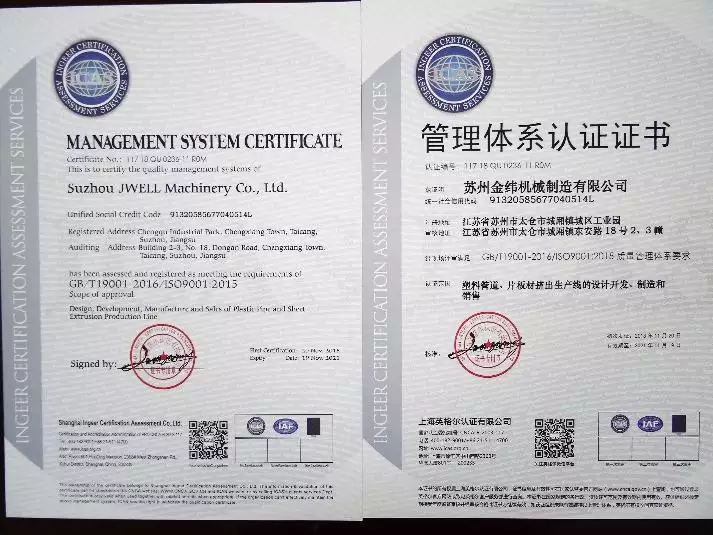
Certified By:Other
Design, Development, Manufacture and Sales of Plastic Pipe and Sheet Extrusion Production Line
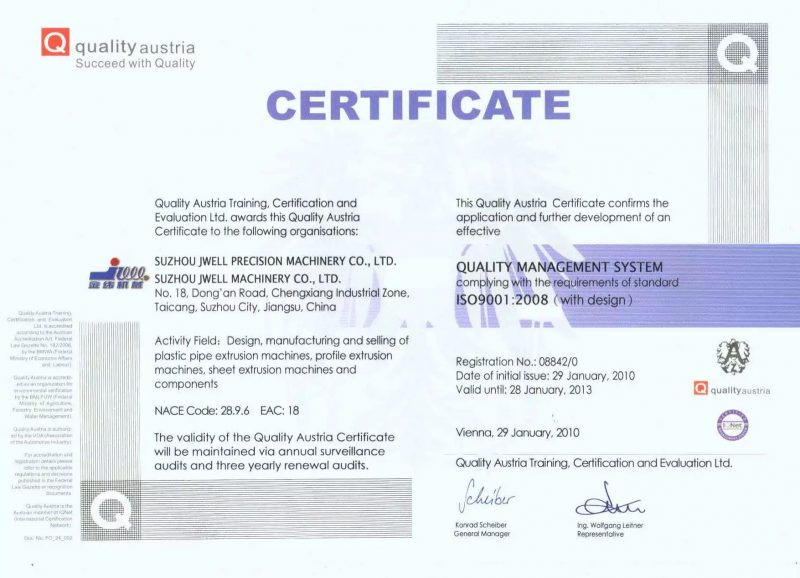
Certified By:Quality Austria Training, Certification and Evaluation Ltd
Plastic extrusion line